Even the most top-of-the-line building materials can fail over time if they’re not properly installed according to manufacturer specifications. Whether you’re working with traditional tapes, liquid-applied flashing, or metal kick-out flashing, it’s crucial to follow best practices to ensure long-lasting performance.
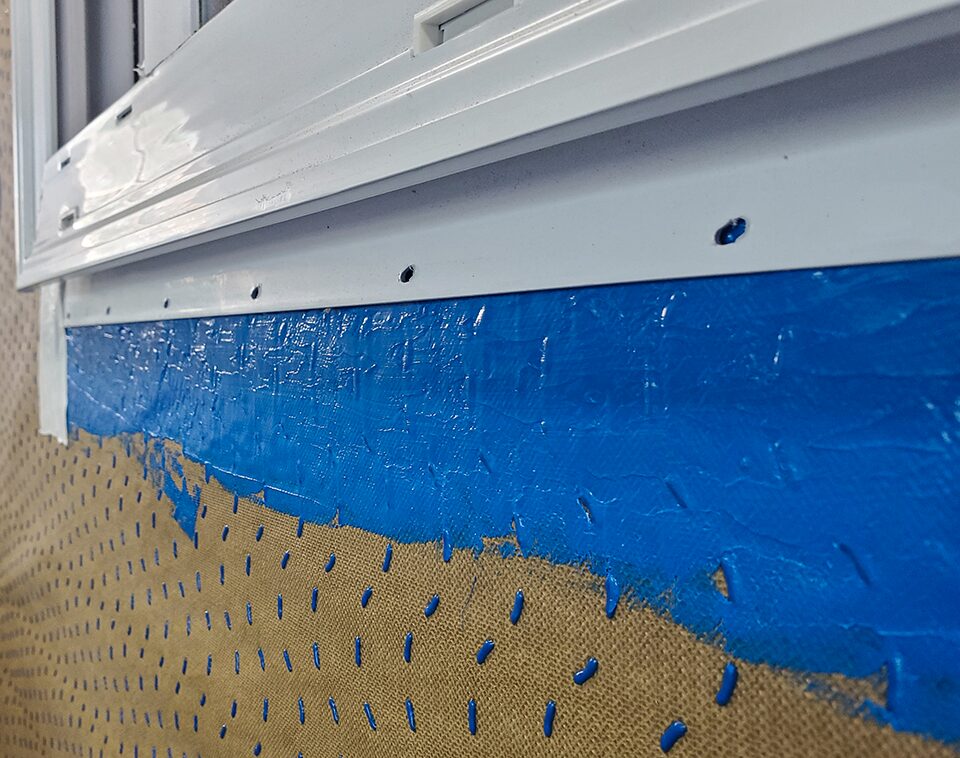
Benjamin Obdyke, a leading supplier of moisture management products and innovations, explores a few strategies to ensure performance and longevity.
- Choose Quality Materials: Often, homeowners allocate plenty of their budget for more visible items in the home, such as granite countertops and high-end fixtures. But downgrading to the cheapest, least-labor-intensive options for the building envelope can lead to very visible problems down the road; materials that degrade will lead to moisture problems and rot. For example, using a liquid-applied flashing such as HydroFlash LA is a slightly higher cost but can better address difficult-to-flash areas that are most prone to problems, such as around windows. Invest up front for long-term durability.
- Follow Manufacturer Instructions: The makeup of flashing and housewrap materials can vary greatly from manufacturer to manufacturer as well as from product to product. It’s important to understand the nuances of installing each flashing brand and type—from pressure requirements to exposure limitations—to ensure performance and maintain warranties. This also includes checking for compatibility with other materials the product may come into contact with on the home.
- Use Correct Overlaps: Proper sequencing with a shingle overlap at all intersections is one of the most critical steps to ensuring moisture flows down and away from the wall system.
One problem area, for example, is where the roof and the wall meet. In the ideal approach to a direct roof-to-wall intersection, the roofing contractor should install the roofing membrane first, extending the membrane 12 inches up the wall at the intersection and install shingles with metal step flashing and kickout flashing at the eave. Then the siding installer will apply the wall’s weather resistant barrier, shingle-lapping the weather resistant barrier over the kickout flashing so that water flows down and out rather than under the layers.
- Plan Ahead for Roof Penetrations: Failure to plan ahead for challenging obstacles, such as the chimney and pipe boots, can lead to MacGuyver-ing flashing. Communicate with installers about how those areas will be flashed and sequenced, how the masonry will be cut, etc. to ensure proper practices are followed.
- Apply Proper Pressure: Many of today’s self-adhered flashings are designed to stick for a long time—but only if the installer applies proper pressure. Some adhesives require pressure activation, so be sure to follow manufacturer instructions. This is one of the biggest mistakes our field reps see on a regular basis—and one of the easiest to avoid.
- Account for Exterior Insulation: For projects using exterior foam board insulation, the added thickness will affect your window flashing because the window may be sitting flush with the continuous insulation or may have a deeper recess. You’ll need to adjust the application of your housewrap and flashing accordingly. (Check out this blog post to learn how to address this potential issue.)
Above all, proper flashing relies on similar principles as the rest of the envelope: plan ahead, sequence properly, and use a systems approach. Following manufacturer best practices can make a dramatic difference in the performance of your wall and roof systems.
For more information on Benjamin Obdyke products, visit www.benjaminobdyke.com.
ABOUT Benjamin Obdyke
Since 1868, Benjamin Obdyke has been helping architects, builders, and contractors in the United States and Canada Build Better™ by developing and adding new advances to its product line. Benjamin Obdyke develops, sources, markets, and sells proprietary roof and wall products that improve the building envelope and the performance of other building materials for the new construction, repair, and remodel markets. Innovations from Benjamin Obdyke, such as the first roofing ridge vent on a roll, the first wood roofing underlayment, and the first rolled product to provide drainage and air flow in rainscreen wall assemblies, have helped shape today’s building practices. Headquartered in Horsham, Pa., Benjamin Obdyke partners with a network of distributors, dealers, buying groups, and cooperatives to reach building professionals in the United States and Canada. For more information, visit www.benjaminobdyke.com.